
The passenger recognition and sharing module (PRSM) identifies the current occupant status of the vehicle by using a body pressure sensor and CNN, shares the information with surrounding vehicles, and computes the optimal steering angle using passenger information and road information. The road roughness classification module (RRCM) classifies the roughness of the road by using the pressure data applied to the suspension and the K-NN algorithm and computes the optimal brake pressure. The BDDS proposed in this paper consists of two modules. This paper proposes a braking-pressure and driving-direction determination system (BDDS), which computes the brake pressure and steering angle optimized for passenger safety by utilizing more diverse information than existing autonomous vehicles. However, the self-driving technology that is currently completed focuses only on perfect driving and does not guarantee the safety and comfort of passengers. The numerical results provided by the updated model show a satisfactory accuracy.Ī fully autonomous vehicle must ensure not only fully autonomous driving but also the safety and comfort of its passengers.
Forklift equilibrium 3d update#
The measured data are exploited for model update and validation. An experimental campaign is designed and conducted to asses the vehicle behavior when running on the obstacle, by measuring the vibrations of the chassis and of the mast, as well as the forces generated by the mast tilting actuators. It takes into account the ground/tire interactions, by means of a simplified nonlinear contanct model, and the load handling assembly dynamics. A model of the complete forklift is developed inside a commercial multibody environment. In particular, this study focuses on a specific test condition, namely the passage on a steel plate obstacle at constant speed, which is one of the most severe maneuvers of the reference cycle in terms of dynamic loads. The research aims at developing numerical tools based on multibody models to predict accurately the dynamic loads acting on the forklift in the conditions of interest.
Forklift equilibrium 3d verification#
This work deals with the analysis of the dynamic response of a counterbalance forklift truck prototype when performing standard verification maneuvers, defined by the manufacturer’s testing protocols.
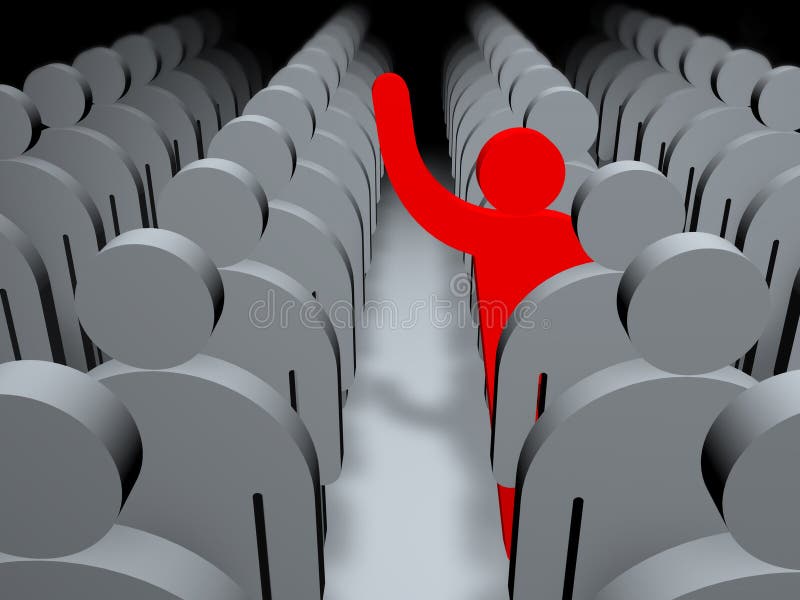
It gives a deep view of the nature of striated yaw marks’ formation and can be applied in any program for the simulation of vehicle dynamics with any level of simplification.

The mark-creating model shows good compliance with experimental data. It was validated in the program developed by the author, in which the vehicle is represented by a 36 degree of freedom multi-body system with the TMeasy tire model. The model is universal, i.e., it applies to a tire moving along any trajectory with variable curvature, and it takes into account the forces and torques which are calculated by solving a system of non-linear equations of vehicle dynamics. A mathematical model of how the striations will appear has been developed.

They can be used: (a) in a macro-scale for establishing the vehicle’s positions and orientation as well as an estimation of the vehicle’s speed at the start of yawing (b) in a micro-scale for inferring among others things the braking or acceleration status of the wheels from the topology of the striations forming the mark. Tire yaw marks deposited on the road surface carry a lot of information of paramount importance for the analysis of vehicle accidents. Hence, the modelling and validation strategies are proven viable and effective. After model updating, the results provided by the numerical simulations match the experimental data satisfactorily. Experimental tests are conducted on the forklift to measure the vehicle vibrations when running on the obstacle, for model validation purposes. To this end, a preliminary model of the complete forklift, featuring rigid bodies and a simplified tire–ground contact model, is implemented with a commercial software. Indeed, unlike most of the other wheeled vehicles, forklifts typically do not have advanced suspension systems and their dynamic response is significantly affected by ground irregularities. It focuses on a specific test, namely the passage of a speed-bump-like obstacle at high velocity, which represents one of the most severe conditions within the reference cycle.
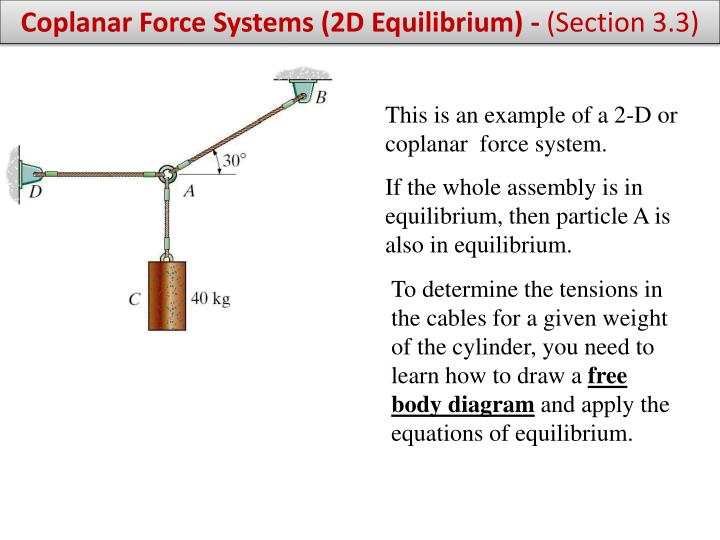
This work aims at defining sufficiently accurate and easy-to-implement modelling approaches and validation procedures. The final objective is creating virtual testing tools based on numerical multibody models to evaluate the dynamic stresses experienced by the forklift family of interest during a reference operating cycle, defined by the manufacturer’s testing protocols. This study investigates the dynamic behavior of a recently developed counterbalance forklift truck.
